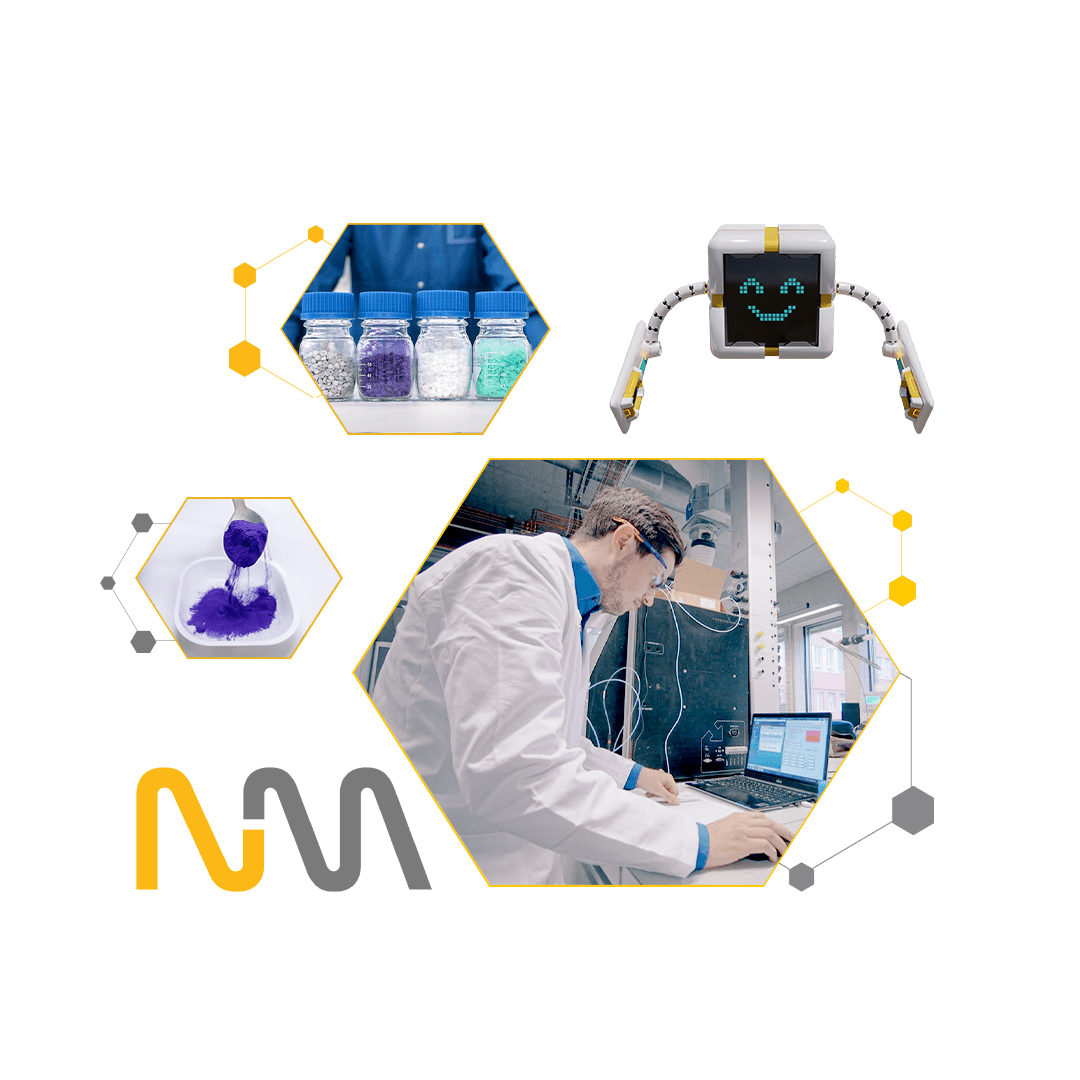
ABOUT US
Your strategic partner for innovative
MOF-based solutions
novoMOF focuses on the development, the production and the commercialization of metal-organic frameworks (MOFs). These highly porous adsorbents offer competitive solutions to global problems such as carbon capture, water scarcity, and food waste.
OUR TECHNOLOGY
A core focus of novoMOF is Carbon Capture
We’re pioneering a revolutionary solution to fight CO₂ emissions using Metal-Organic Frameworks, or MOFs. Our materials are a game-changer for both the climate and businesses.
Join us in creating a greener, more sustainable future. Reach out to novoMOF today to empower your business success with CO₂ capture.
Solution Process
1
SELECTION
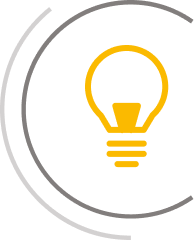
Your business challenges drive us in the identification of the right MOFs.
2
SYNTHESIS
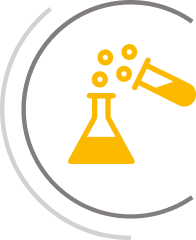
You receive synthesized MOFs at the highest quality.
You can test them for your application.
3
OPTIMIZATION
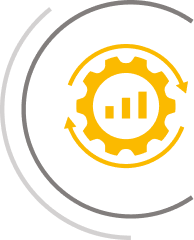
You benefit from support in optimizing the performance of your process.
4
PRODUCTION
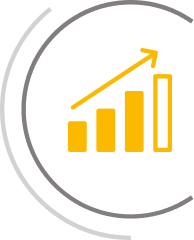
You leverage your commercial application with us, your trusted supply partner.
We scale production according to your needs from grams to tons.
WHY US
VALUE-FOCUSED
HIGH-QUALITY
EXPERTISE
SCALABLE
INNOVATIVE
Network
TESTIMONIALS
novoMOF is a reliable partner for any organization seeking to scale up their metal-organic frameworks. As the principal investigator of our Atmospheric …

David R. Moore, Ph.D.
– GE Research Executive Manager, Carbon Capture Technology Leader
I had the opportunity to work with novoMOF AG on the scale up of one of our MOFs. Their production of a high-quality MOF at kilogram scale,…
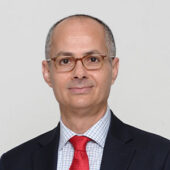
Dr. Omar M. Yaghi.
– Professor of Chemistry, UC Berkeley
In our syngas conversion development efforts at Dow we have been investigating MOFs as catalyst precursors. In order to evaluate and compare our internal …
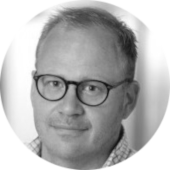
Matthijs Ruitenbeek
– Senior R&D Manager The Dow Chemical Company
As the chief scientific officer, I am always scouting for new technology platforms to improve our products at Silent-Power AG. I’ve met novoMOF at a conference in …
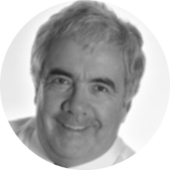
Dr. Reto Holzner
– Chief Scientific Officer econimo DRIVE
Recent Posts
novoMOF Blog Blog about Metal-Organic Frameworks (MOFs), their application and related industries.
- Decarbonizing Glass Manufacturingon June 25, 2025 at 2:10 pm
The glass industry, a cornerstone of construction, automotive, and packaging sectors, is also one of the most energy-intensive and CO₂-emitting industrial processes. With global climate regulations tightening and demand for sustainable products on the rise, manufacturers are actively seeking practical and cost-effective solutions to reduce CO₂ emissions. In this blog, we explore why MOFs are ideally suited to the unique challenges of glass production and how they offer a competitive edge in an increasingly regulated and carbon-conscious global market. Why is CO₂ capture relevant for the glass industry? A major challenge for the glass industry is that about 30% of its CO₂ emissions come from the breakdown of raw materials like limestone and soda ash during melting. These emissions are hard to avoid, because they are part of the chemical process—not from burning fuels. This means that even if the industry switches to renewable energy, this portion of emissions will still occur. As a result, glass manufacturers may still face carbon taxes or regulatory costs for emissions they can’t eliminate with cleaner energy alone. This makes it even more important to explore effective CO₂ capture solutions. Are MOFs a good fit? Glass manufacturing involves high-temperature processes that inherently generate significant CO₂ emissions. These emissions come from two main sources: Combustion of natural gas or other fuels to heat furnaces. Decomposition of raw materials (especially carbonates like soda ash and limestone) during glass melting. Typical CO₂ concentrations in these gases range from 8 to 12%, ideal for adsorption-based capture systems. Post-combustion capture at these concentrations provides a balance between feasibility and cost-effectiveness, making it one of the most attractive strategies for industrial decarbonization. However, a key challenge in glass flue gas is humidity. Moisture levels typically reach 10–15%, which can degrade the performance of conventional adsorbents like zeolites or amine-based systems. Most glass furnaces employ only basic flue gas treatment primarily cooling and particulate filtration, without dehumidification. This is where MOFs show a distinct advantage. novoMOF’s hydrothermally stable MOFs retain their structural integrity and adsorption performance even in high-moisture environments. This eliminates the need for expensive upstream drying, simplifying system integration, and reducing installation complexity. Integrating MOF systems in glass manufacturing facilities Furnaces and forehearths in glass manufacturing generate large amounts of low-grade heat, which often goes unused or is only partially recovered. This generates an opportunity for MOF-based systems. MOFs can be regenerated at just 90°C, allowing them to tap into this waste heat stream. This integration: Minimizes external energy input Reduces operating costs Enables modular, space-efficient systems suitable for retrofitting existing plants Unlike traditional solvent systems that require tall columns, high-pressure compressors, or complex refrigeration loops, MOF-based units are lightweight, flexible, and scalable. The result is a flexible and cost-effective carbon capture system that aligns with both the thermal profile and operational constraints of glass manufacturing. Meeting climate policies through CO₂ capture
- Towards carbon-neutralityon April 2, 2025 at 1:28 pm
Companies around the world are under growing pressure to reduce their carbon footprint and align with global sustainability goals. Governments and regulatory bodies are tightening emission standards and giving priority to businesses that demonstrate environmental responsibility. Achieving carbon neutrality has evolved from a corporate social responsibility initiative to a strategic necessity. This blog aims to help understand key aspects to achieve carbon neutrality, from carbon accounting to implementing reduction strategies to help companies navigate the transition toward a more sustainable future. CO₂ Neutral vs. CO₂ Negative When discussing carbon emissions, two key terms often come up: CO₂ neutral and CO₂ negative. While both indicate a commitment to reducing environmental impact, they represent different levels of action and ambition. CO₂ Neutral (Carbon Neutral): A company is considered CO₂ neutral when it balances the amount of carbon dioxide it emits with an equivalent amount removed from the atmosphere. This is typically achieved through emission reductions, increased efficiency, and carbon offsetting projects, such as reforestation or renewable energy investments. The goal is to achieve net-zero emissions, meaning the company does not contribute additional CO₂ to the atmosphere. CO₂ Negative (Carbon Negative): Going beyond neutrality, a CO₂ negative approach means that a company actively removes more carbon dioxide from the atmosphere than it emits. This can be done through advanced carbon capture technologies, large-scale reforestation, or direct air capture projects. Being CO₂ negative results in a net reduction of atmospheric CO₂, contributing significantly to reversing climate change. For companies, striving for CO₂ neutrality is often the first step in sustainability efforts, while CO₂ negativity represents a more ambitious goal for those aiming to have a positive environmental impact. Accounting for carbon emissions The first step towards carbon neutrality is to go through the identification process for accounting carbon emissions. The Greenhouse Gas (GHG) Protocol, the leading global standard for carbon accounting, categorizes emissions into three scopes based on their source and level of control by an organization. These scopes aim to help companies track and manage emissions systematically, allowing better reporting, regulatory compliance, and targeted mitigation strategies. Scope 1: Direct emissions. These emissions come from sources owned or controlled by the company. This scope includes production or process equipment to generate heat, steam, and electricity, such as boilers and furnaces, and mobile combustion equipment like vehicles. Scope 2: Indirect emissions. This scope includes emissions from the use of electricity generators not owned or controlled by the company (purchased electricity). Therefore, the emissions occur at the facility where electricity is generated. Scope 3: Other indirect emissions. This category includes emissions from downstream and upstream processes used by third parties along the value chain of a company. Scope 1 and 2 emissions are managed by the company through equipment selection and choosing their suppliers. Therefore, addressing scope 1 and 2 emissions is the starting point to tackle. Scope 3 emissions are harder to control and require collaboration with partners and suppliers. Implementing Reduction Strategies: Steel Manufacturing Example
- Unlocking the industrial potential of MOFson January 21, 2025 at 3:27 pm
Metal-Organic Frameworks are one of the most exciting materials of recent decades for the chemical industry. After the development of the first MOFs, one of the biggest challenges was to make them accessible for different processes. Their unparalleled surface areas, tunable porosity, and chemical versatility have enabled applications in gas storage, carbon capture, catalysis, and beyond. However, despite their potential, MOFs are not yet accessible on an industrial scale. Here, we aim to take the discussion further and explore what it truly means to make MOFs accessible at an industrial scale—and how we are achieving that vision. Industrial-Scale MOFs: What Does It Mean? The first step in producing MOFs is in the lab, on the gram scale. Industrial-scale production means producing MOFs at the kilotonne (kt) or megatonne (MT) level. The scale-up process does not just involve increasing the size of a reactor, but also requires considering critical factors such as: Raw material sustainability Production efficiency and robustness Product quality and performance retention Ease of downstream processing Achieving success in the scale-up process requires combining expertise and a profound understanding of MOF chemistry and engineering. How We Do It From years of experience, we conclude that scalability depends on one key factor: recipe stabilization. This means transforming fragile, lab-scale recipes into robust, reproducible processes. The stabilization process addresses every aspect of production including: Raw Materials and MOF Compositions: Raw materials are prioritized based on sustainability, ensuring a low environmental footprint from the start. They are also readily available, eliminating bottlenecks in the supply chain. For more on how MOFs contribute to the circular economy and address sustainability challenges, see our blog: Circular Economy - Tackling Challenges with Novel Materials. Solvents for Reaction, Work-Up, and Shaping: Traditional MOF recipes rely on toxic and expensive organic solvents like dimethylformamide (DMF). Organic solvents are avoided wherever possible, replacing them with greener alternatives. This shift improves safety, reduces costs, and aligns with global sustainability goals. Reaction Conditions: Key factors like pressure, temperature, additives, and reaction times are optimized to ensure: Reproducibility: Consistent results across batches. Efficiency: High yields with minimal waste. Scalability: The ability to use conventional manufacturing equipment at atmospheric pressure and low temperatures. Product Quality: Maintaining—and even improving—MOF performance at scale requires fine-tuning the synthetic procedure. For instance, adjustments in crystal size, porosity, or defect density can significantly impact gas adsorption, catalytic activity, or mechanical stability. For more insights, see our blog about How We Measure and Ensure the High Quality of Our MOFs. Product Rheology: Once produced, the MOF powder must be easily processed into its final form—whether as granules, coatings, or nanofibers. Our approach ensures that the as-synthesized material can transition seamlessly into application-specific formats without compromising quality or functionality. Learn more about how particle size affects MOF performance and processing in our blog: Particle Size of Metal-Organic Frameworks. Example of improved product rheology (left: big agglomerates make downstream processing more challenging; right: novoMOF's methods yield in MOFs in fine powder, comparable to baking flour, that facilitates further processing) A Recipe for Industrial Success